Over the past decade, the 3D printer has become an essential tool for architects in bringing great ideas to life. But in the age of COVID-19, design studios across the country are elevating their 3D printers to serve a higher purpose: manufacturing face shields, a first line of defense for healthcare workers on the front lines of the coronavirus pandemic. While N95 masks are considered the gold standard of protection against the virus, face shields can extend their shelf life, protect the face and eyes from airborne droplets and compensate where N95 masks are in short supply. They can also readily be printed in mass quantities with the right guidance and a healthy supply of filament.
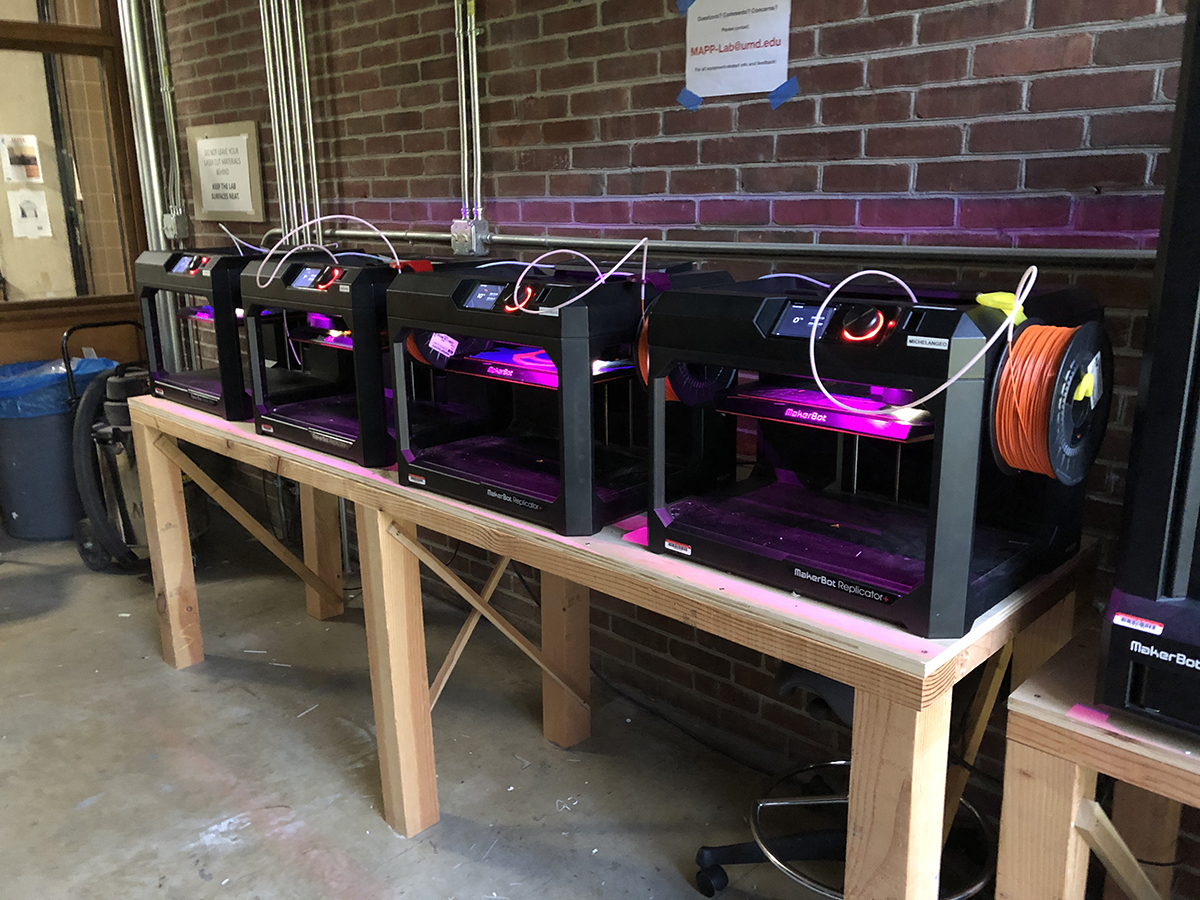
Using a National Institutes of Health (NIH)-sanctioned blueprint provided by Prusa, MAPP alumni and students join a growing legion of citizen servants who are pivoting their technology to address critical shortages in personal protective equipment (PPE), which continues to plague hospitals and first responders nationwide. “When you have a firm with the wherewithal to pull this off and people willing to do it, well, of course we had to do it,” said Ayers Saint Gross Architect and Associate John Kucia (B.S. Architecture ’09, M.ARCH ’11).
About face: For alumni at Ayers Saint Gross, unity thrives with a renewed purpose
The emails started circulating in March. Maryland Governor Larry Hogan had just declared a state of emergency in response to the growing COVID-19 pandemic when employees at Ayers Saint Gross, a Washington/Baltimore-based design firm, started talking about a grassroots initiative to make face shields. Open Works, a non-profit makerspace in Baltimore and frequent Ayers Saint Gross partner had put out the call to action: any company or firm that had a 3D printer and was willing to donate time and resources, could produce face shields using an optimized template provided by the Czech company Prusa. Printed shields would be collected centrally at Open Works and distributed to health care workers nationwide. The groundswell of enthusiasm behind the idea—which would essentially transform Ayers Saint Gross’ model rooms to mini production facilities—was quick to grow to consensus and openly embraced by Ayers Saint Gross leadership. But there were a lot of moving parts: materials were one, but equally important were the critical protective material the Ayers Saint Gross team would need as part of the required sanitary production standards. The scarcity of gloves, bleach and masks threatened to stymie the project before it even got off the ground. So, Ayers Saint Gross’ maker team started spreading the word among the Ayers Saint Gross community. News also traveled among friends and colleagues on social media. Within days, hundreds of rubber gloves, masks, bottles of bleach and rubbing alcohol had been donated to the cause. “I think the team effort is maybe just as much a part of this story,” said Kucia. “It was an incredible internal community effort.”
Over the past two weeks, 100 shields have been produced in Ayers Saint Gross’ Washington and Baltimore offices. Many of the people at the helm of production are UMD alums, including Eli Shanklin (B.S. Architecture ’14, M.ARCH ’17), Sam Polinik (B.S. Architecture ’04), Daniel Lucenti (B.S. Arch 09’), Timothy Shook (M.ARCH ’18), Russell Holstine (M.ARCH ’16) and Kucia. The team works in shifts to sanitize the space and equipment, replace parts, refill material, produce masks and prepare them for shipment to Open Works.
While Kucia says community has always been an integral focus of Ayers Saint Gross’ mission, the pivot of their space has created new resolve during such uncertain times. It has also brought their notoriously tight-knit profession even closer; Ayers Saint Gross is just one of several firms who have reinvented themselves to produce face shields for healthcare workers; a slack channel set up by Open Works, as well as social media has created a forum for colleagues across firms to share pro tips, sanitation supplies and materials. When the printers at Gutierrez Studios went down, they donated all of their filament to Ayers Saint Gross. Ayers Saint Gross recently donated alcohol to another firm who needed it to get their efforts off the ground. The experience, Kucia says, has nurtured a culture of community bringing former classmates, colleagues and, yes, competitors together under a common mission.
“A lot of the people that I’ve been having conversations with are competitors, but that never comes up. The first thing that comes up is, ‘How are you on materials? Do you need any gloves? How quickly are you printing?’ There may be a little healthy competition about how many of these face shields we produce every day but the whole mentality of competing firms has never come up. It’s actually been an interesting community experience inside the firm and outside. I think it’s one of the really nice things to come out of the COVID-19 crisis.”
MAPP students join UMD COVID efforts to produce face shields for region’s health care workers
Springtime at the University of Maryland is typically marked by the frenzy of mid-term projects, the return of UMD’s farmer’s market and the hordes of students descending on McKeldin Mall to soak in the region’s first stretch of good weather. But 2020 has been anything but typical; the surge of the COVID-19 virus, which shuttered campus in mid-March, has turned UMD into a virtual ghost town. Yet deep in the darkened studio spaces of MAPP, the whirling hum of the school’s 3D printers breaks the eerie silence as a handful of students, donning masks and gloves, churn out a little bit of hope in these very strange times. As part of a campus-wide effort spearheaded by the A. James Clark School and Terrapin Works, four architecture students from MAPP’s ROOTS Home and Abroad student service group are leveraging the school’s five printers to manufacture face shields for medical teams on the front lines of the COVID-19 pandemic.
“This experience allows us to use the resources we have to fight COVID 19 by providing our first responders with equipment that may save their lives while they save ours,” said senior architecture student Carlos Bucio-Marin, president of ROOTS Home and Abroad. Bucio-Marin is working with fellow seniors Ruying Lu, Carissa Mejia and Peter Zhu on a nearly daily basis to produce shields at the school, which are added to shipments routed to MedStar Washington Hospital Center and other area healthcare workers.
The shield design printed at UMD is a modified blueprint approved by the NIH, tweaked to be more comfortable and for reuse. With MAPP’s printers running every day, the ROOTS team is able to churn out around 35 each week to add to the UMD weekly shipment.
“It’s written in the Talmud that by saving one life, you save a world,” says Architecture Professor Ronit Eisenbach, who connected the ROOTS students to Terrapin Works’ efforts and is overseeing the students virtually. “Each shield we can produce not only protects a hospital worker, it protects the people around them, it protects their family. When the outbreak started, we knew we wanted to find a way to help. We are very proud to be involved and making a difference.”
Do you have a 3D printer? NIH offers face shield blueprints and full instructions on their website for anyone interested in contributing PPE to their community. Read more about UMD’s COVID 19